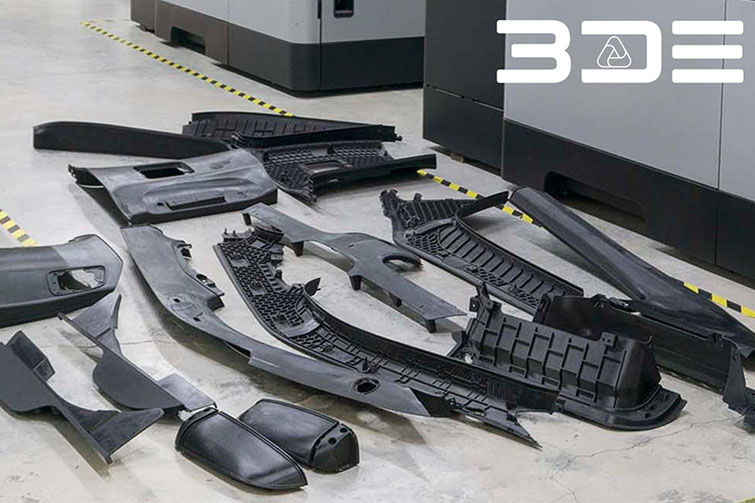
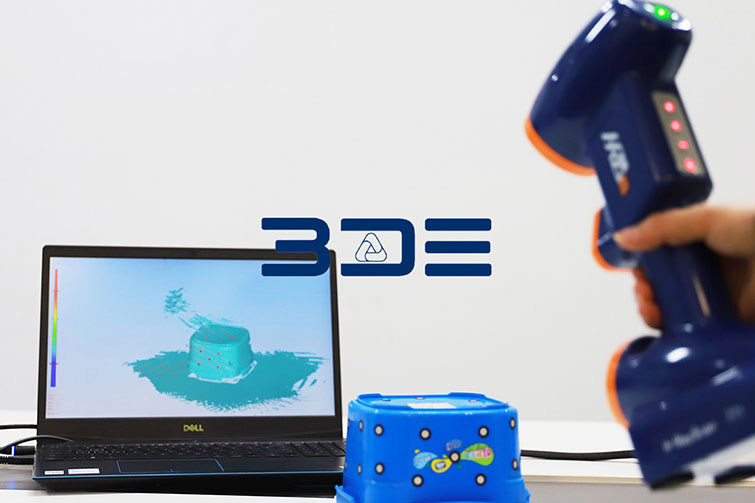
Samples to Drawings to Mass Production
You may have the same question:
I have plastic samples but no 3D drawings. How can I achieve mass production?
This is possible. We can provide product duplication services. Below is the journey from a sample to a set of molds and thousands of identical products.
Step 1. We need scan the sample to a 3D model, this is called 3D scanning. With a 3D scanner, Engineer can effortlessly capture accurate measurements of existing samples or products. This level of precision minimizes errors and maximizes efficiency, ultimately saving time and resources. The shape of the product is scanned into a 3D document, which is usually saved in .igs, .stp and other formats. These formats use common 3D software. For example, UG, PROE, and SOLIDWORKS can be opened. After copying the number, check whether the dimensions in the 3D drawing file are consistent with your sample. There will usually be small errors within the acceptable tolerance range.
Step 2. Once the 3D drawing confirmed, design team will start product analysis. It mainly analyzes whether the product structure can be smoothly demoded when the mold is opened, whether there is back buckle, whether the remolding slope is sufficient and the position of the glue nozzle, use cold runner or hot runner. Then, usually, we will create 2D drawings to check all the critical dimensions. The dimensions and tolerances of each critical component will be marked and need the customer to confirm. A dimensions check report will be generated based on the 2D drawings file to confirm whether the product dimensions are consistent with the original model.
Step 3. After completing the above steps, we can start designing the injection mold. 3d mold structure diagram will clearly show the overall structure of the mold. The 3D mold will be divided to mold parts drawings; the 3D drawing is converted into a 2D drawing and distributed to the tooling shop as a mold master. The 3D drawing file should be sent to the CNC machining department, where the CNC programmer will edit the mold core and the mold opening program to enter the CNC machining center.
Step 4. Based on the received drawings, the mold manufacturing shop will start processing the mold base, drilling and transporting water, ejector pin holes and screw holes. Mold blanks are usually purchased as standard products, and LKM is the most commonly used.
Step 5. After all processing is completed, assembles all components and inspected to see if it fits properly. The tooling can put on the injection machine to run the trail shot. The first Trial is called T1, the second Trial is called T2, and so on. Usually, 3 trials will be enough. Any non-conforming parts will be reviewed and improved. After the trial mold has no problem, the mold will be qualified and suitable for mass production.